From supporting local machine builders to taking on massive, fast-tracked national projects, Egan Company’s UL 508A Panel Shop is proving there’s more to control panels than meets the eye. Under the leadership of Kevin Bodem, the Panel Shop team is building more than custom control panels—they’re building smarter systems, stronger relationships, and scalable solutions for customers across industries.
Designed, Built, and Delivered
With a team capable of full-service design and fabrication, Egan’s panel group can handle it all—designing and building panels from scratch, fabricating to customer specs, or providing Design/Assist support. “One-third of what we do is customer-designed builds, one-third is full Egan design, and the other third is high-volume, repeat production work,” said Bodem.
These control panels take many forms—motor control, power distribution, PLC, and more—and are customized to meet the specific safety, functionality, and installation needs of each project. Regardless of application, every panel is built to UL 508A standards, ensuring quality and compliance.
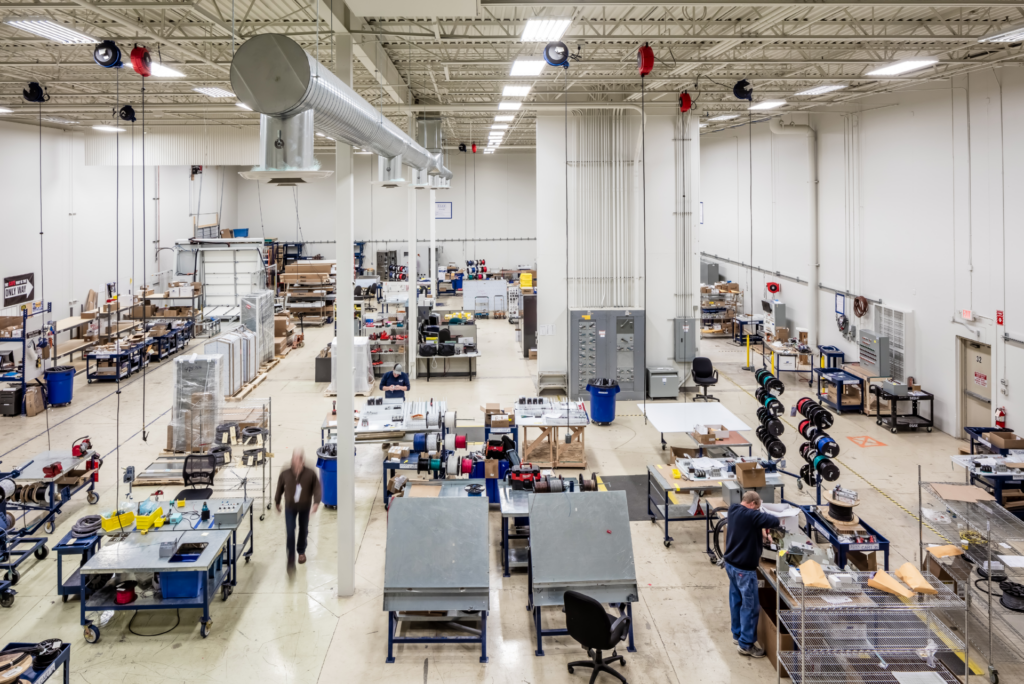
“UL 508A means the panels meet a nationally recognized safety standard,” Bodem explained. “It’s not just about passing inspection—it’s about knowing the product will operate safely in the field.”
Tackling Complexity with Agility
While most builds wrap up in a matter of days, some projects push the limits of what’s possible. A recent project for a long-time partner required hundreds of panels—Egan’s largest panel project to date—and came with tight timelines, post-pandemic supply chain hurdles, and an evolving scope. “It was a year-and-a-half effort from PO to final shipment,” said Bodem. “It took creativity with scheduling, manpower, and sourcing, but we worked closely with the customer and delivered on every front.”
Egan’s flexibility is one reason customers keep coming back. “We’re not just building panels—we’re offering solutions. We can design, fabricate, install, program, and support the entire system. A lot of people don’t realize that until they walk through our building.”
Tools, Tech, and Transformation
Automation continues to play a growing role in Egan’s production process. The shop features automated wire processing and enclosure machining, supported by an industrial engineering team dedicated to process improvement and advancing automation development. This team also serves as Egan’s quality group, ensuring consistent and high-performing results across all projects.

Beyond technology, Egan’s people remain the foundation of the shop’s success. Their expertise drives continuous improvement, from thorough equipment evaluations to collaborative engineering. Robust quality assurance processes, including inspections, and testing help deliver dependable products while identifying opportunities to enhance workflows. Together, these practices ensure each project meets the highest standards and supports customers with solutions built on experience, innovation, and precision.
Support Beyond the Shop Floor
Panel support doesn’t end when a product leaves the shop. “We’re always available when customers call,” said Bodem. “If something goes wrong, we stand behind it. That’s just who we are.” And with Egan’s service team and electricians located across the region, issues are resolved quickly. For OEM partners, Egan acts as a true extension of their operation, often supporting them through multiple product evolutions.
Industries Served—and Miles of Wire Run
Egan’s control panels serve a wide range of sectors, including food and beverage, data centers, packaging, organics recycling, and more. The team works closely with engineers at customer sites to ensure every need is accounted for and every risk is minimized before a panel is powered on.
This year, the shop is on track to produce about 5,000 panels—breaking last year’s record of 4,300 panels.
Powering More Possibility
Whether it’s a one-off build or an enterprise-scale rollout, the Panel Shop team ensures each project reflects Egan’s promise: to be there when it matters and deliver smarter, safer systems that stand the test of time. “We’re not just a Panel Shop,” said Bodem. “We’re a systems integrator, an electrical contractor, and a solutions partner—all in one.”