Building in Brooklyn Park pending purchase agreement with local medical device developer
MINNEAPOLIS, MN – Specialty trades contractor Egan Company announces the consolidation of its Twin Cities facilities in preparation for becoming a hybrid workplace.
Following a year of enabling remote work for many office employees—due to the COVID-19 pandemic and local Executive “Work from Home” Orders—the Company’s need for two office locations in the Twin Cities has decreased significantly. Its 126,000 square foot Brooklyn Park, Minn. facility is pending a purchase by a local medical device developer. This location has been Egan’s headquarters since 2003.
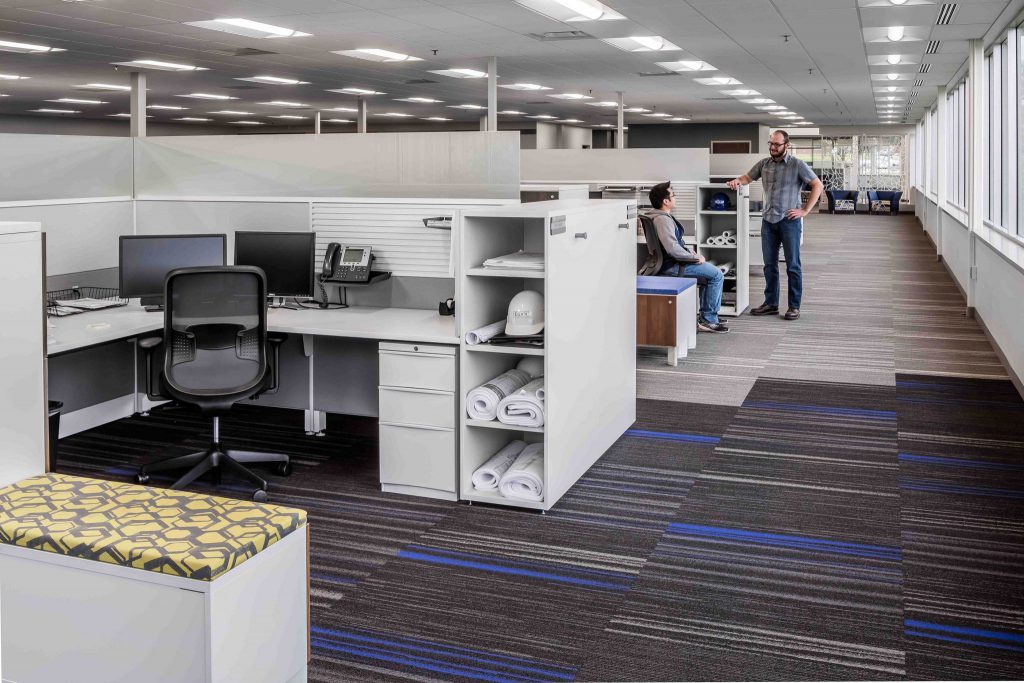
Egan’s Champlin, Minn. location will become the Company’s new headquarters and the designated hub for flexible workspace and collaboration. The 200,000 square foot space was purchased in 2015 and underwent a full renovation to fit business growth needs. It currently houses 145 workspaces, fabrication shops, garage, and warehouse.
Consolidation readiness renovations will take place within the Champlin facility over eight weeks and result in collaborative enhancements, new conversation rooms, a training center, additional breakroom, and outdoor recreation space. Over 60% of the existing workspaces will be converted to flexible/hybrid. An additional 27,000 square feet will be left unfinished to allow for additional office growth flexibility and shop expansion. The first phase of this consolidation of Egan’s Twin Cities offices will be complete by Fall 2021.
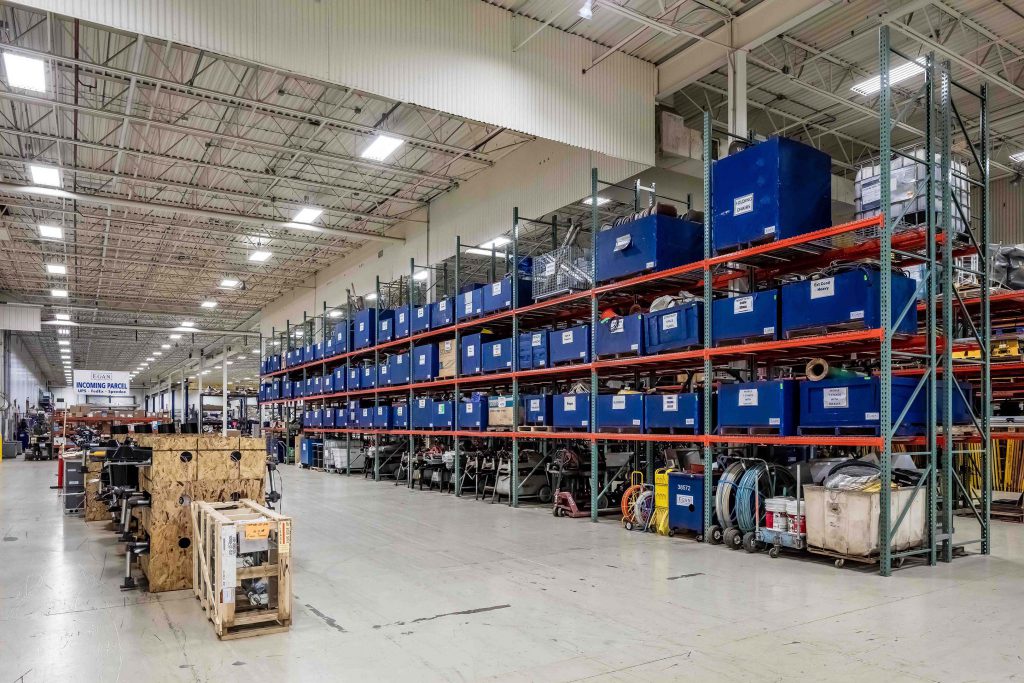
Employees will continue to work from locations that best fit their role and schedule, including jobsites, customer facilities, fabrication shops, or a home office.
Egan also operates in a Southern Minnesota location in Rochester.
About Egan Company
Egan Company is a privately-owned, specialty contractor providing building trades to general contractors, engineers, building owners, property managers, and facility engineers. Specialties include: electrical, mechanical, curtainwall/glazing/metal panels (InterClad), millwrights, building technology, controls and system integration, and 24/7 service. Egan serves every stage of a building and provides in-house expertise in planning, design and engineering, construction, and maintenance. For more information about Egan Company, visit www.eganco.com.
# # #